With 3D printing against the pandemic
With 3D printing against the pandemic
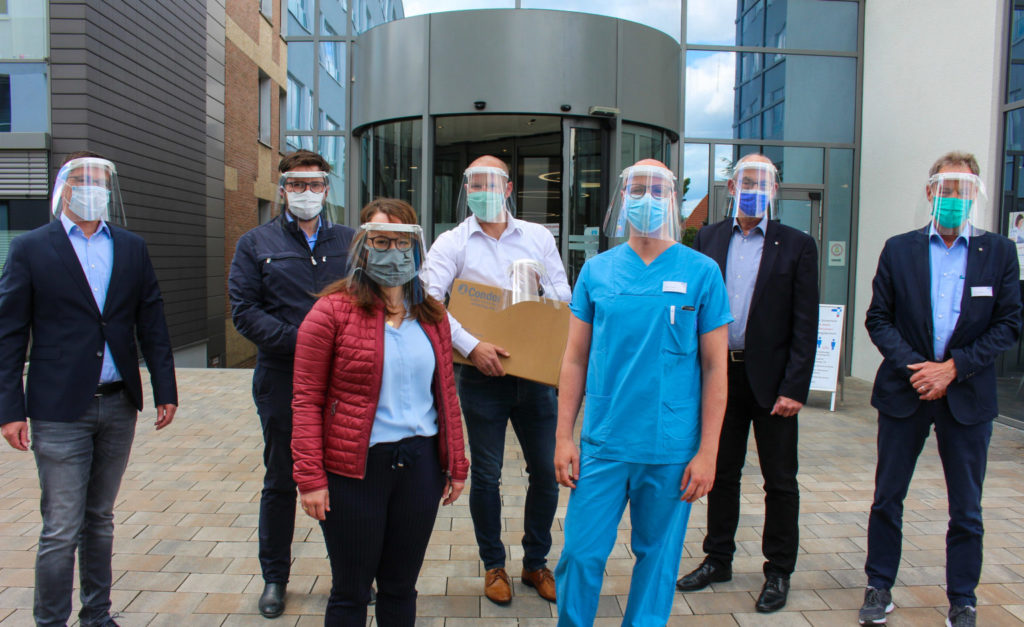
Paderborn researchers and regional project partners produce 4,500 face shields for healthcare facilities in OWL
Since April 27, masks have been mandatory in Germany. While homemade face coverings are also permitted for private use, masks in the health care sector, on the other hand, must meet stricter minimum requirements. So that there are no shortages precisely where they are most urgently needed, a regional project team has developed and produced face shields.
Paderborn researchers and regional project partners produce 4,500 face shields for healthcare facilities in OWL
Masks have been compulsory in Germany since April 27. While homemade face coverings are permitted for private use, masks used in the healthcare sector must meet stricter minimum requirements. So that there are no shortages precisely where they are most urgently needed, a regional project team has developed and produced face shields. The team includes scientists from the University of Paderborn as well as the companies Condor Group, Centroplast Engineerings Plastics and LST laser cutting technology. A total of up to 4,500 of the so-called "Faceschields" are to be delivered free of charge to hospitals, doctors' practices, nursing homes and other healthcare facilities in the OWL region. The Brüderkrankenhaus St. Josef in Paderborn has now received its delivery. Interested facilities could contact info@condor-group.de to place an order.
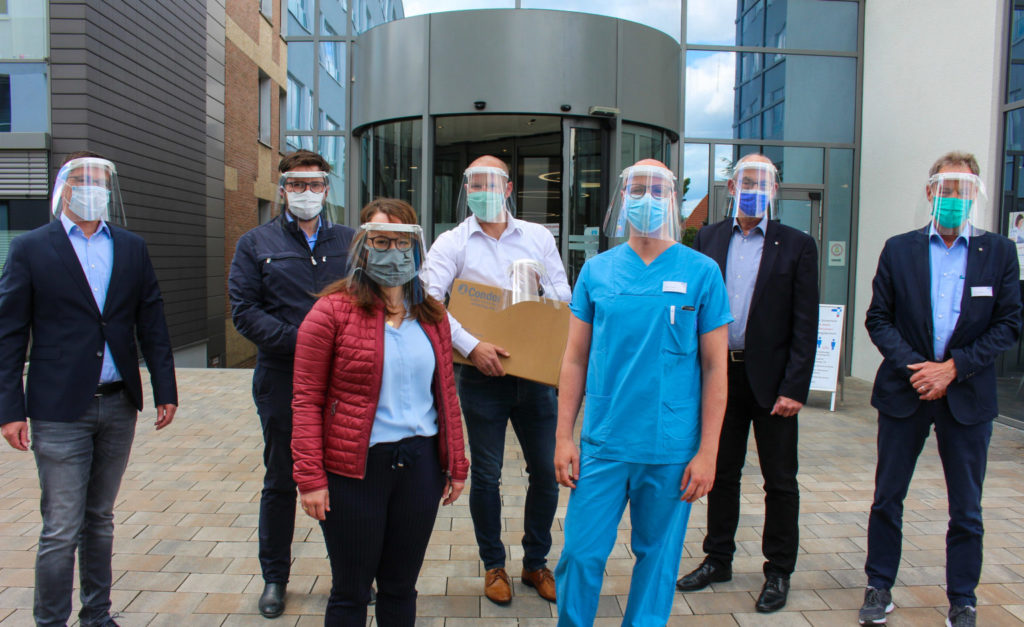
Involved are scientists of the University of Paderborn as well as the companies Condor Group, Centroplast Engineerings Plastics and LST laser cutting technology. A total of up to 4,500 of the so-called "Faceschields" are to be delivered free of charge to hospitals, doctors' practices, nursing homes and other healthcare facilities in the OWL region. The Brüderkrankenhaus St. Josef in Paderborn has now received its delivery. Interested facilities could contact us at info@condor-group.de for an order.
Innovation engine 3D printing
Additive manufacturing processes, also known as 3D-Duck, are attracting increasing interest in science and industry. At the University of Paderborn, the "Direct Manufacturing Research Center" (DMRC) is a research institution that aims to industrialize precisely these processes. Together with the Condor Group GmbH, doctors and specialist nurses for anaesthesia and intensive care medicine, four DMRC scientists have formed a core team to supply the region with industrially produced face shields using additive manufacturing processes. The powder needed for production was donated by Eos GmbH and Evonik Industries AG. Dr.-Ing. Christian-Friedrich Lindemann, Managing Director of the DMRC and coordinator of the four-member research group, is pleased with the result: "The current example shows wonderfully that additive manufacturing can provide local substitutes in the short term for otherwise globally established supply chains."
Face plates meet high requirements
In the early phase of the project, the participants first obtained an overview of the current market in video conferences and discussed ideas, prototypes and possible medical applications. Finally, the decision was made to manufacture face shields. An important criterion for the project team: the face shields, which are worn in addition to the mouth-nose protection in everyday clinical practice, must meet the medical and hygienic requirements of a hospital. Ira Fecke-Schulte , Managing Director at the Condor Group: "On the one hand, the face shields must be easy to disinfect. On the other hand, they must be one-size-fits-all to be suitable for many head sizes. In addition, they should of course be comfortable to wear, safe and easy to remove. In this respect, it was also important for us that the wearers do not have to assemble the face shields themselves, apart from the headband." To ensure all of this, they tested several prototypes and gathered feedback from users to further optimize the development process. DMRC developer Christian Schumacher, who came up with the design, played a major role in this.
Print templates to copy
The plastic PET (polyethylene terephthalate) was used in the production of the protective film, in which the companies Centroplast and Laserschneidtechnik were involved. The film is half a millimetre thick and measures 23 by 37 centimetres, which is recommended by the developers as the optimum size for use in hospitals. In addition to supplying face shields, the DMRC is making the design files available free of charge for rebuilding at the www.dmrc.upb.de/content/downloads .
"From the region - for the region"
The project was made possible by the medical technology initiative "From the region - for the region". The DMRC and the Condor Group launched the initiative, which has since been joined by other partners. Together they want to make a contribution to society and to the protection of medical personnel.